In the manufacturing of home appliances like refrigerators, washing machines, and air conditioners, the WC – 3.0 plays a crucial role. These appliances have complex electrical systems with numerous wire connections. For instance, in refrigerators, the machine is used to rivet and connect the wires that power the compressor, control the internal lighting, and manage the temperature sensors. The 3000kg crimping force ensures that the connections made with copper belt terminals are extremely secure, capable of withstanding the vibrations and temperature changes during the appliance’s operation. The integrated processing of copper belt terminals, which involves cutting, shaping, and crimping in one step, helps manufacturers save time and reduce material waste, thus lowering production costs.
For small electrical appliances such as electric kettles, toasters, and hair dryers, the WC – 3.0 offers reliable wire connection solutions. These devices require precise and safe electrical connections within limited internal spaces. The machine’s ability to handle different wire thicknesses, thanks to the 8mm adjustable height, allows for customized processing. By using copper belt terminals processed by the WC – 3.0, manufacturers can ensure that the electrical connections in small appliances are durable and free from issues like cold soldering, which could lead to electrical failures or safety hazards. The availability of straight and bent die holders also enables the machine to adapt to the diverse design requirements of various small appliances.
In the production of smartphones and tablets, where miniaturization and high – precision electrical connections are key, the WC – 3.0 is indispensable. It is used to connect the fine – gauge wires in components such as batteries, charging ports, and circuit boards. The machine’s riveting – based wire processing method provides a more reliable connection compared to traditional soldering, especially in preventing issues caused by thermal stress during the device’s operation. The high – quality copper belt terminals processed by the WC – 3.0, with their strong tensile strength after riveting, ensure that the electrical connections remain stable even under the constant movement and flexing that these portable devices endure.
For laptops and desktop computers, the WC – 3.0 is utilized for wire connections in power supply units, motherboards, and internal cabling. The machine’s compliance with safety standards like UL and JIS is crucial, as these standards ensure that the electrical connections in computer systems are safe and reliable. The 23mm stroke and 3000kg crimping force allow for the secure connection of wires with different cross – sectional areas, ensuring stable power transmission and signal integrity within the computer. The integrated processing of copper belt terminals also speeds up the production process, enabling manufacturers to meet the high demand for computer products.
Automotive wiring harnesses are complex networks of wires that require extremely reliable connections. The WC – 3.0 is employed to process the wires in these harnesses, which connect various electrical components in a vehicle, including the engine control unit, headlights, taillights, and interior electronics. The machine’s powerful crimping force and precise riveting ensure that the copper belt terminal connections can withstand the harsh automotive environment, including vibrations, temperature fluctuations, and exposure to moisture. The waste – free production process of copper belt terminals helps automotive manufacturers reduce costs, while the availability of different die holders allows for the customization of wire – terminal connections according to the specific requirements of different vehicle models.
In the rapidly growing field of electric vehicles, the WC – 3.0 is essential for the production of components such as battery packs, electric motor controllers, and charging systems. EVs have high – voltage and high – current electrical systems, and the reliability of wire connections is of utmost importance. The machine’s ability to create strong and durable connections with copper belt terminals ensures the safe and efficient operation of these components. The 8mm adjustable height feature allows for the processing of wires with different thicknesses used in EV components, while the integrated terminal processing function improves production efficiency, helping EV manufacturers meet the increasing market demand.
Industrial control panels, which are the nerve centers of automated production lines, rely on the WC – 3.0 for secure wire connections. The machine is used to process the wires for components within these panels, such as relays, switches, and programmable logic controllers (PLCs). The 3000kg crimping force ensures that the copper belt terminal connections are stable and can withstand the electrical currents and mechanical stresses in industrial environments. The intuitive operation and compact design of the WC – 3.0 make it easy to integrate into the production of control panels, while the compliance with safety standards provides peace of mind regarding the reliability and safety of the control systems.
For robotic systems used in industrial automation, the WC – 3.0 is used to connect the wires in components such as motors, sensors, and control circuits. Robots require precise and reliable electrical connections to ensure smooth operation and accurate movement. The machine’s high – quality riveting and copper belt terminal processing provide the necessary strength and stability for these connections. The availability of different die holders allows for the customization of wire – terminal connections to fit the specific design requirements of various robotic systems. The efficient and waste – free production process of the WC – 3.0 also contributes to the cost – effectiveness of robotic system manufacturing.
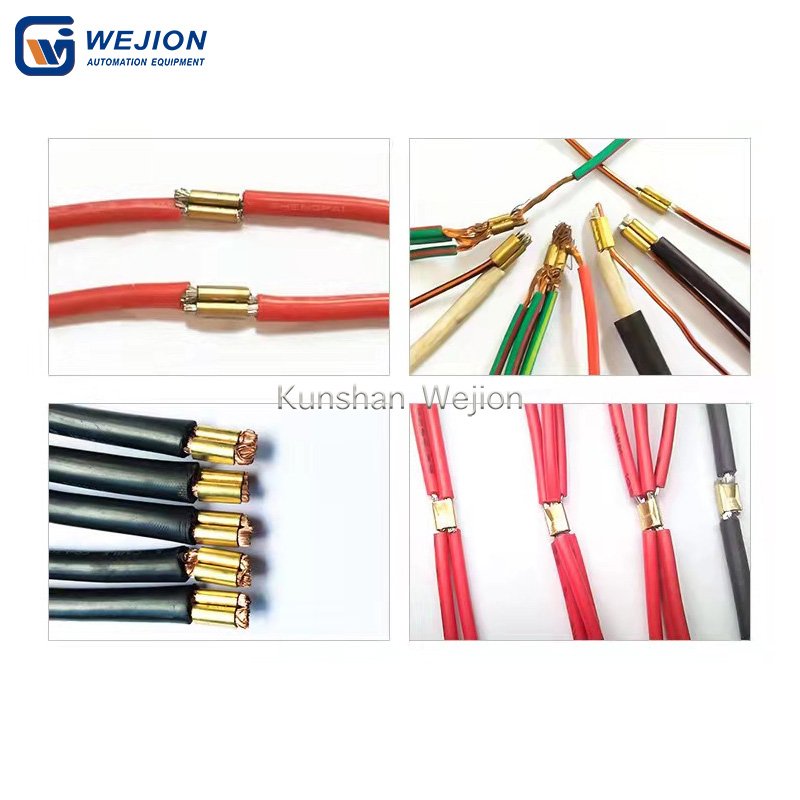